THE BENEFITS
Improved Safety
According to Safe Work Australia, workplace injuries cost employers, workers and the community over $61B per year. Employers have legal obligations under work health and safety laws to:
Identify hazards in the workplace
Assess the risk those hazards create
Eliminate or minimize them as much as possible
Typically, forms are used to manage the hazards, and depending on the industry could be referred to as a “Job Hazard Analysis” (JHA), “Job Safety Analysis” (JSA) or a “Take 5”.
The problem with paper-based safety forms are:
The worker needs to carry blank forms with them, if he runs out the JHA may not be performed, and there will be no record.
Completed forms need to be returned to the depot and stored for future reference if required (or re-keyed into an electronic system) – there is a risk that forms are lost (eg. Placed on a dashboard and blown out of the window).
Auditing and retrieval of safety information if required can be difficult.
When new safety issues are identified it can take time to update and distribute new forms.
Retriever Mobile can incorporate electronic safety forms that are integrated into the workflow of the mobile application.

Retriever safety forms offer the following solutions:
Enforceability within the application workflow – if the worker does not complete the JHA then they are prevented from progressing to the next stages of the job. If the JHA identifies that the site risk is too high it can instruct the worker to leave the site until it is remediated.
Faster completion time – with paper forms workers are required to manually enter their name, date and site address details each time they complete a form – the electronic form can pre-populate the details making it faster to complete.
Logical workflow that reveals questions that are relevant to previous answers – for example if the worker is not working at heights then questions related to harnesses, ladders etc. don’t need to be answered.
Hazard linkage to control measures – within the workflow when a hazard is identified then the application can present the logical control measures – for example the use of Personal Protection Equipment (PPE).
Time and location stamping – along with the worker’s signature, the electronic form is “stamped” with both time and GPS data which can prove when and where the form was completed.
Photographs – can be taken and recorded within the safety form providing documentary evidence of an issue.
Immediate safety report generation – once the form is completed an electronic pdf report (including signatures and photographs) can be immediately emailed to both internal staff and also to customers in conjunction with a service report.
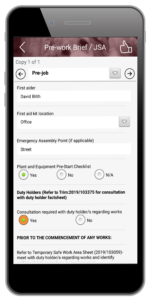
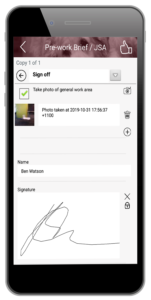